Ingersoll Tools GmbH has integrated VERICUT® into the digital process chain
Small lot sizes – short delivery times. There’s no better way to describe the greatest challenge the global manufacturing industry is facing.
How do you address it?
Perfection in production, as one example, is the foundation for sustainable competitiveness.
This is why Ingersoll Tools GmbH has been using the leader in NC simulation, VERICUT, since 1996 as the interface between NC programming and production.
Thanks to VERICUT, this full-service provider in the machining industry can load in their tools, clamp their workpieces, and start production without fear of scrapping parts or machine collisions. Errors are detected during simulation, before actual machining.
“No program goes into production without VERICUT,” says CAD/CAM manager, Susanne Klamma. “And in combination with our own software ITM Builder, the simulation saves us a lot of time and worry.”
Handling the risks at Ingersoll is not an option, but a requirement. At the Haiger headquarters alone, up to 90% of the tools are special orders with lot sizes ranging from 1-3.
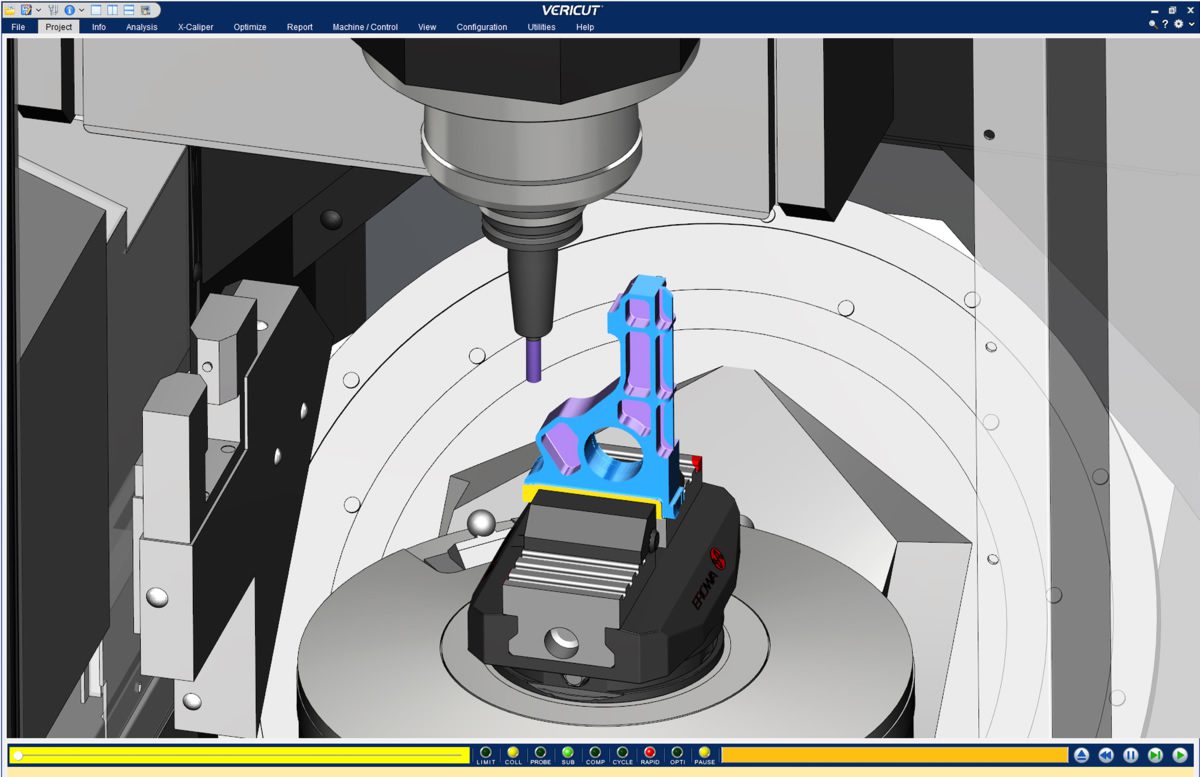
Ingersoll Tools GmBH
Ingersoll Tools GmbH essentially produces milling and drilling tools with indexable inserts in standard and special designs, re-grindable milling tools, carbide indexable inserts, HSS and carbide knives, tool holders, tool clamping devices, and thread whirling systems.
In addition to the standard program, Ingersoll, with its three German sites in Haiger, Vaihingen-Horrheim, and Wulften, develops milling cutters, drills, turning, and grooving tools according to customer requirements. The company’s products are used worldwide. Ingersoll, a member of the Iscar International Metalworking Companies (IMC) since 2000, is present across industries such as aerospace, railway manufacturing, gearing technology, shipbuilding, and mold and die.
The automotive industry in particular often has demands for special tools, such as those for machining engine blocks, crankshafts, or steering knuckles.
The Ingersoll workflow from design to machine presents itself as a state-of-the-art process chain. The tool is completely designed with Creo in 3D. The 3D models stored in the PDM (product data management) system and are then used by the NC programmers to develop the NC program, which is also done in Creo.
Klamma, who has been responsible for the administration and development of the CAD and CAM systems at Ingersoll since 1989, states:
“When programming the NC paths, the programmers select the required production tools from a central, proprietary SQL-based tool database. Then a software that was also developed in-house is called up, which fully assembles the production tools.”
The NC program with all the required tools is then checked in VERICUT® for possible collisions.
“[VERICUT is] an essential part of our process chain,”
Says Klamma, who is also responsible for the development of post-processors and the DNC connection to production machines. Finally, a program is called up that creates the setting sheet with all the information for the machine operator. Logistical information about the tool can also be called up from the PPS (production planning and control) system.
Digitally in Detail
Ingersoll reduces the complexity of its development, project planning, and production by utilising digital end-to-end processes.
This corresponds to both tight timeframes and the high-quality standards of the company. Proven standards and automations replace repetitive work, even with small batch sizes. The consistency, continuity, and quality of the data is secured several times over.
Klamma explains,
“In the first step, the NC programmer creates his NC program in Creo/NC only with the actual tool, such as the milling cutter or drill that suits his machining. The NC programmer receives support from our in-house developed tool database when he’s choosing the tool.”
He then calls up the ITM Builder software. This assembles the optimal combination of tools and holders for the selected production machine according to specific rules.
“Here, of course, the NC programmer also has the option of influencing the assembly process.” says Klamma, “NC programmers don’t have to stick with this approach.”
The rules for assembling complete tools can be adapted to the needs and specifications of production and can be changed without modifying the NC program itself. Finally, the programmers bring up VERICUT with all the necessary information from the ITM Builder interface. Klamma states:
“The machine and control is loaded with the NC program, the raw part, and the workpiece holder, and exact representations of the assembled tools.”
Integration in the process chain
Ingersoll has a long tradition of dealing intensively with VERICUT. In Haiger and at almost 20 other IMC locations around the world, VERICUT, the industry standard for NC simulation, has been in use for decades.
Klamma explains,
“At the Haiger site, we mainly manufacture special tools in very small batch sizes. Due to short delivery times, we cannot afford to produce rejects or spend a lot of time trying things out on the machine. Everything on the machine has to run collision-free immediately.”
Operators standing at the machine and checking whether production is running collision-free or swivelling the A-axis in advance as a test are a no-go at Ingersoll. The actual backup is VERICUT.
“When simulating the programs,” says Klamma,
“it is particularly important to us that the NC program is simulated after the post-processor runs, and in the exact form that will be transferred to the machine. Every common NC programming system simulates the program, but always before the code is post-processed. This is why using VERICUT as our own simulation software is so important to us.”
Integrates ahead with ICAM and VERICUT
The use of the combination of post-processor generation in ICAM and NC simulation with VERICUT is quite interesting. The networked process has proven particularly effective when using new CNC machines.
Klamma reports: “ICAM offers the option of creating a generic post-processor using a questionnaire. This is a great advantage when you’re starting with a new machine, since you don’t have to start from scratch. Because the output of the post-processor is very easy to adapt, you can also easily integrate the required control commands for VERICUT, for example.”
VERICUT, however, always has the last word. Klamma explains,
“When we order a new machine, I use the VERICUT simulation to test my post-processor in order to eliminate the worst errors even before the machine is physically commissioned. Even when testing the post-processor, a crash in VERICUT is significantly cheaper than a crash on the brand-new machine.”
Ingersoll has also been working with ICAM for a very long time. Klamma continues,
“The software offers us the necessary flexibility in our environment. For example, data from different CAM systems can be processed. More importantly, I can adapt the output to our needs at any point in the process. So, I can adapt the data for the machine exactly to the needs of the operators.”
Productive manufacturing with Auto-Diff
The goal when introducing VERICUT at Ingersoll in 1996 was to establish a reliable machining process and the simulation of tool movements, with the main focus being on the collision check of the 5-axis machining centers in addition to the machine simulation of complex machining programs. Almost all manufacturing programs at Ingersoll now run through VERICUT’s simulation with verification and analysis.
The VERICUT Auto-Diff module has proven to be particularly effective. In the last step of creating the NC program, the machined workpiece is compared with the part from the design. With Auto-Diff, the NC programmer is then shown exactly where there are gouges or excess material.
“Minimal deviations are accepted,” says Klamma. Any major deviation means that the programmer has to adapt his NC program.”
Minimum Cutter Extension
Klamma continues,
“VERICUT offers us another advantage that we firmly integrate into our process chain. Basically, the tools are always assembled as short as possible to be stable from the beginning. The VERICUT feature ‘minimum cutter extension’ changes the extension length of our tools during the simulation if a collision is imminent but can be avoided.”
Because the ITM Builder reads this information and, if possible, pulls the tool out of the holder or exchanges the holder to get the necessary length. After the adjustment, another simulation is run in VERICUT.
“This cooperation between VERICUT and our software relieves the NC programmer considerably, since the adjustments are made automatically and only to the extent necessary.”
In fact, the long-established interaction of digital process units is reminiscent of the basics of Industry 4.0. Klamma continues:
“We work here with a 3mm distance between workpiece and tool. Our tool presetting knows that the specified length of the tools must not be undercut. And the machine operator can rest assured that no collisions will happen.”
Would you like to become a WEAF member?
As a WEAF member you will get full access to exclusive and valuable information, plus greater networking opportunities.
Being part of the WEAF community means becoming part of one of the largest aerospace, defence and advanced engineering clusters in Europe.
Joining WEAF will bring you exclusive and valuable benefits in all areas of this fast growing industry.